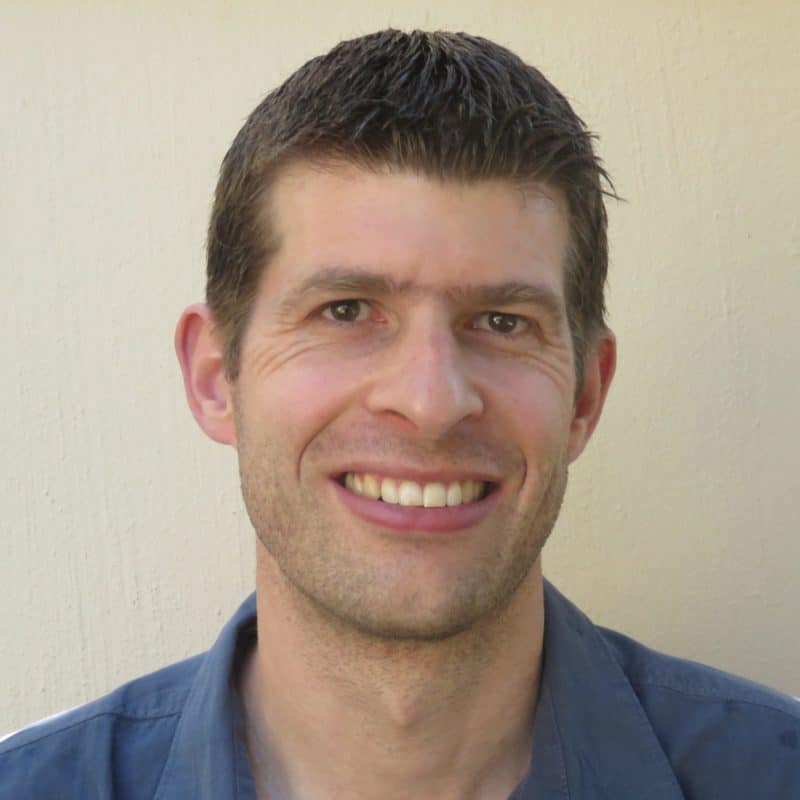
Three major trends – electrification, digitalisation, and automation – offer South Africa’s mining industry the opportunity to increase safety and productivity, and shape ‘the mine of the future’.
South African mining houses must tap into three transformative trends – electrification, digitalisation and automation – as they look to drive greater safety, productivity and sustainability in their operations, while extending the life of their mines.
Globally, the mining industry is already seeing a clear shift from diesel to electrification at mining operations. Greater digitalisation is resulting in increased productivity and more sustainable use of resources while lowering input cost, while automation is increasing productivity and changing the way mines work. Together, these three trends are shaping what we call ‘the mine of the future’.
These three trends are critical success factors for the mining industry to continue its modernisation and meet increasingly stringent environmental and sustainability goals while staying globally competitive. They offer real possibilities, which weren’t available previously, to overcome today’s challenges and ensure a bright future for the mining industry.
Electrification gaining traction
As mines step up their efforts to cut costs and increase efficiency, the supply of energy emerges as one of their biggest challenges. On top of the expense of delivering diesel fuel to remote sites, come also costs for the service, repair and replacement of diesel-powered vehicles and machinery.
The move towards electrification of mining operations is well under way in Europe and South America. An obvious starting point for several miners is to invest in fully electric or hybrid-electric vehicles to lower diesel usage and cut costs and pollution. The Swedish company Boliden is to install an additional 3km of trolley line at its Aitik mine after a successful 700m pilot project plus 1.8km at Kevitsa – and says it will reduce its diesel consumption by 5.5 million litres when its investment is complete.
Other miners going this route include Copper Mountain Mining in Canada. ABB will install its haul truck trolley assist infrastructure to help Copper Mountain achieve a reduction in carbon intensity by more than 50 percent in medium-term with a final target of zero by 2035. The installation, which includes engineering, supply and construction management for a DC substation and an overhead catenary system (OCS), combines ABB’s electrification and automation expertise in the mining industry.
Data: the most valuable resource of all
Data is key for the mine of the future to oversee critical processes and increase the useful life of mines by improving cost efficiency, ore recovery and asset management. Mining companies collect huge amounts of data from their equipment and operations, but this information is hardly used at all to generate insights.
It is crucial for mining companies to have a solid digital strategy in place to ensure well-informed decision-making that will help them maximise energy usage, productivity, reliability and safety, while minimising outages, emissions and costs.
Polish coal miner Bogdanka is developing an Industrial Internet of Things (IIoT) solution that will connect various systems, devices and services. This will allow the mine’s engineering team to predict failures, solve machine and equipment failures and reduce equipment downtime, thus reducing high maintenance costs of mining assets. Cost optimisation is particularly important for the company’s plans to increase production.
The automation imperative
Automation has immense potential to reduce operating costs, improve operations and take people out of harm’s way. Many South African mines are experimenting with technologies like automated drilling and blasting, but they’re only scratching the surface of what’s available.
McKinsey estimates that innovations in artificial intelligence (AI), machine learning and IIoT have the potential to save the mining sector an estimated $373 billion by 2025 by automating machinery operation, facilitating predictive maintenance, improving traceability, harnessing the power of real-time data and analytics, and providing visibility across the mine-to-market value chain.
The mine of the future isn’t one where robots do all the work. Rather, it’s a connected operation where all assets are linked and smart, decision makers can see exactly what’s happening across their operations on a dashboard, and asset management is proactive.
The biggest challenge facing local mines is to get buy-in for the transformation. Because mining is a major employer in communities across the country, there’s a perception that automation and digitalisation will result in job losses. The reality is, profitable mines don’t reduce headcount. If a mine is profitable, the shareholders are going to want to expand and that creates numerous opportunities downstream.